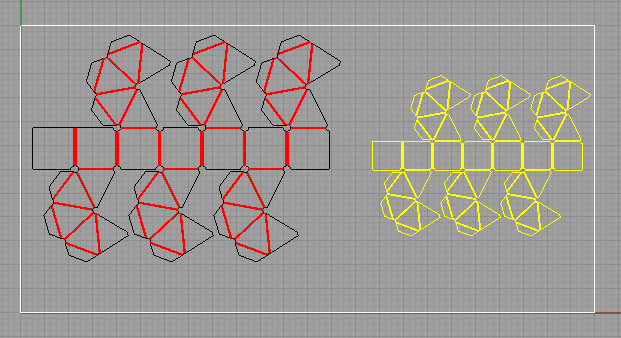
Foundry Research - Paper Patterns
While experimenting with the creation of cardboard cells as a building material for another project, I quickly recognized a connection between this type of pattern-making and its potential application in foundry castings. My initial focus was on the concept of transforming flat materials into three-dimensional forms—an approach inspired by origami techniques for creating structural integrity.
Through this exploration, I realized that I could streamline the traditional pattern-making and casting process by bypassing several conventional steps. Instead of crafting patterns from wood, wax or other materials, I discovered that paper-based patterns could be directly utilized. By dipping these paper forms into a ceramic shell slurry, I was able to create molds. The paper patterns could then be burned out during the firing process, leaving a cavity ready to be filled with molten metals such as bronze, copper, iron, or aluminum. The paper patterns were designed using Rhino a CAD program that helped me develop vector line work that I could use to direct the laser cutter. After they were cut and the fold lines etched it was a simple matter of folding them up and holding them in place by using a bit of melted wax. Gates, sprues and pour cups were then added before being dipped in ceramic shell.
This method simplified the casting workflow and also significantly reduced the need for costly materials and labor-intensive steps typically associated with traditional foundry techniques. What follows are the results of this innovative exploration.
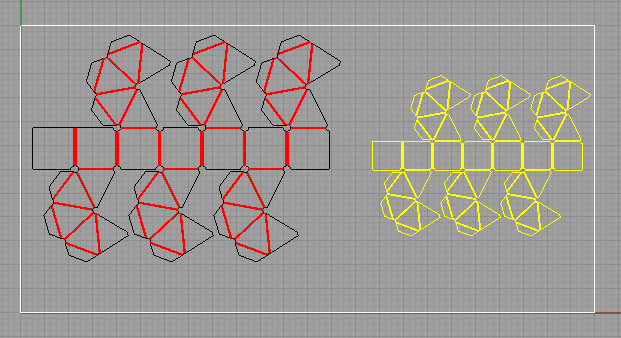
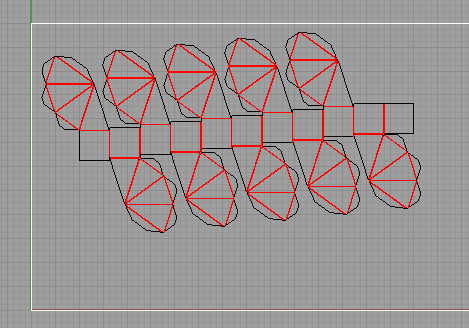
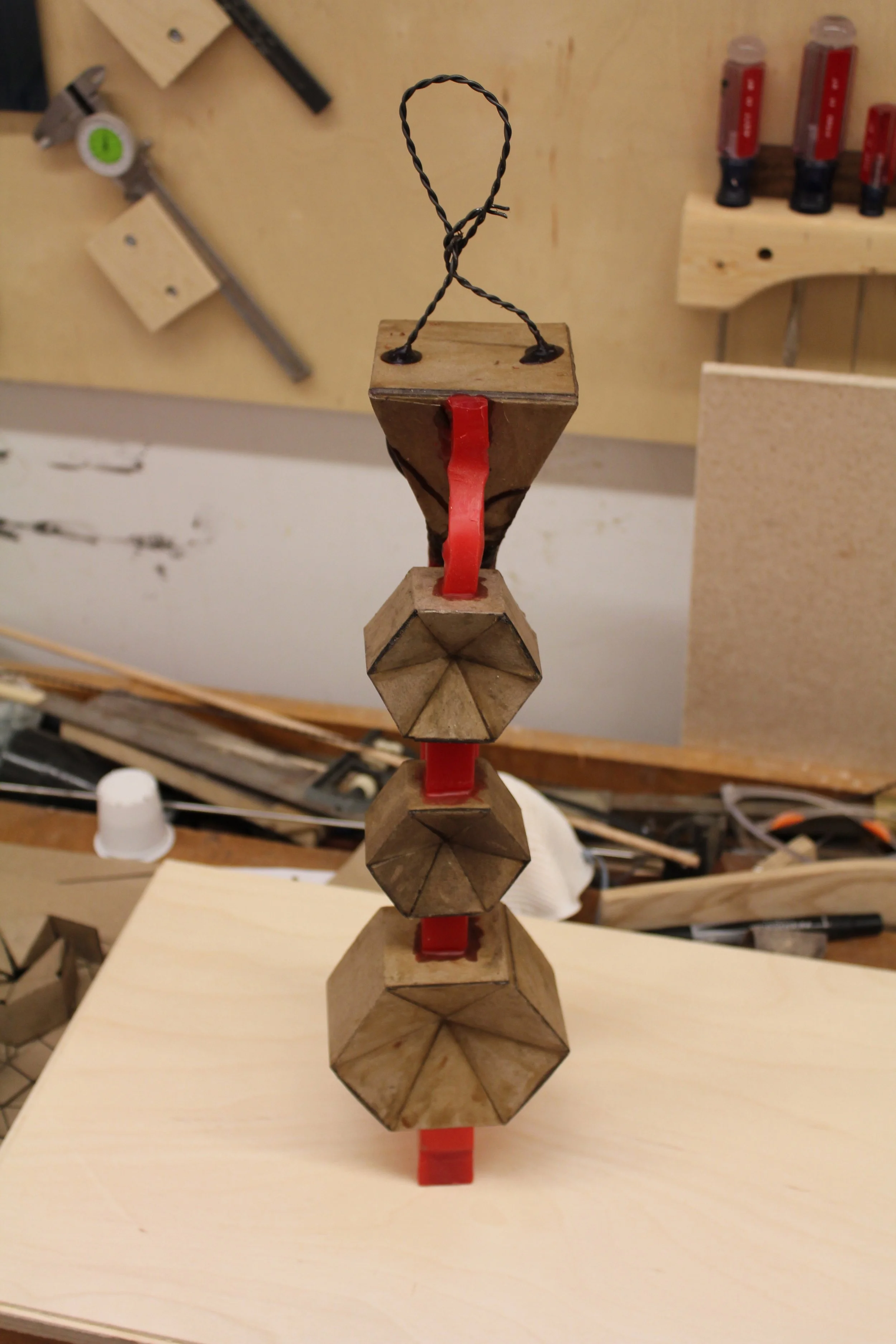
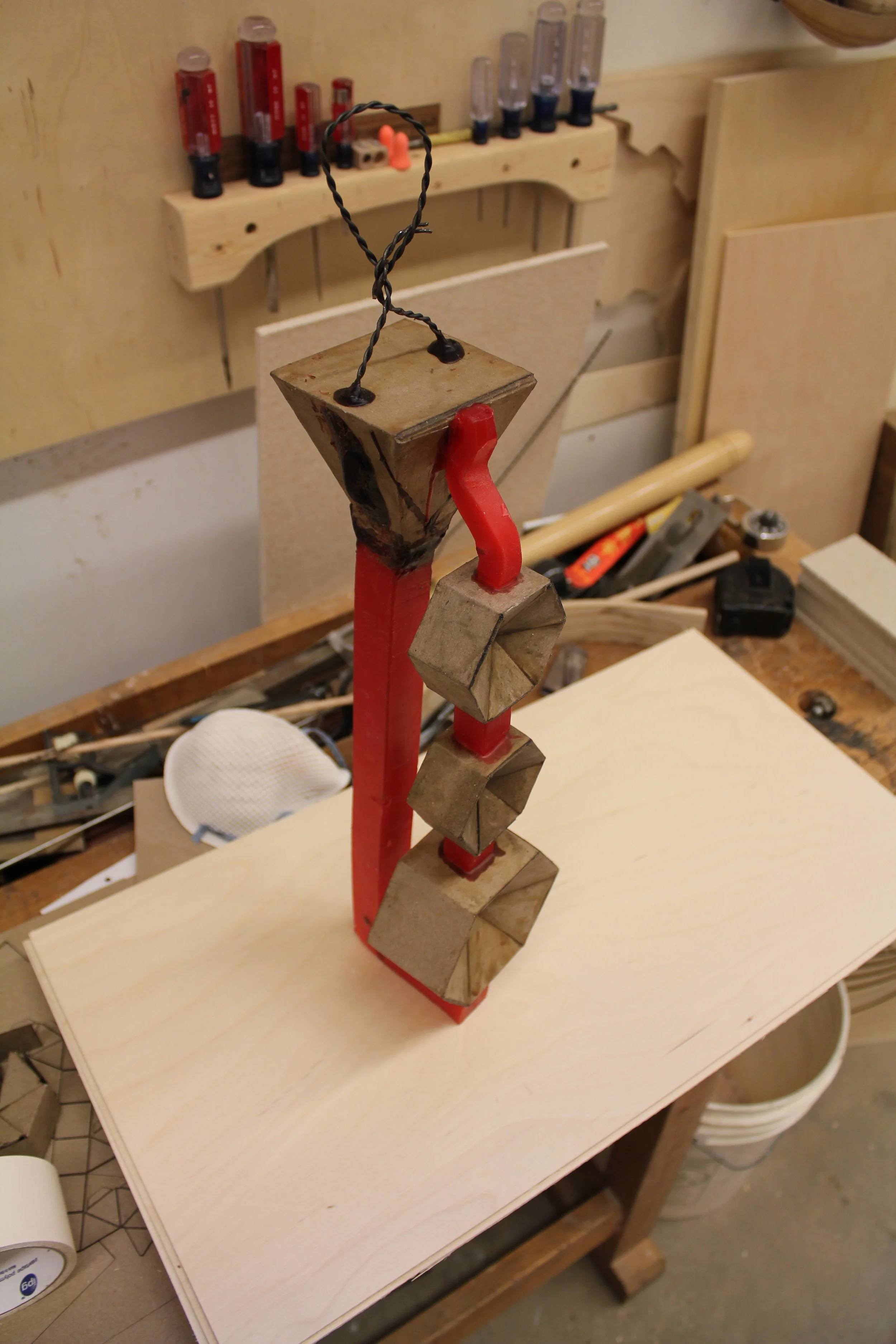
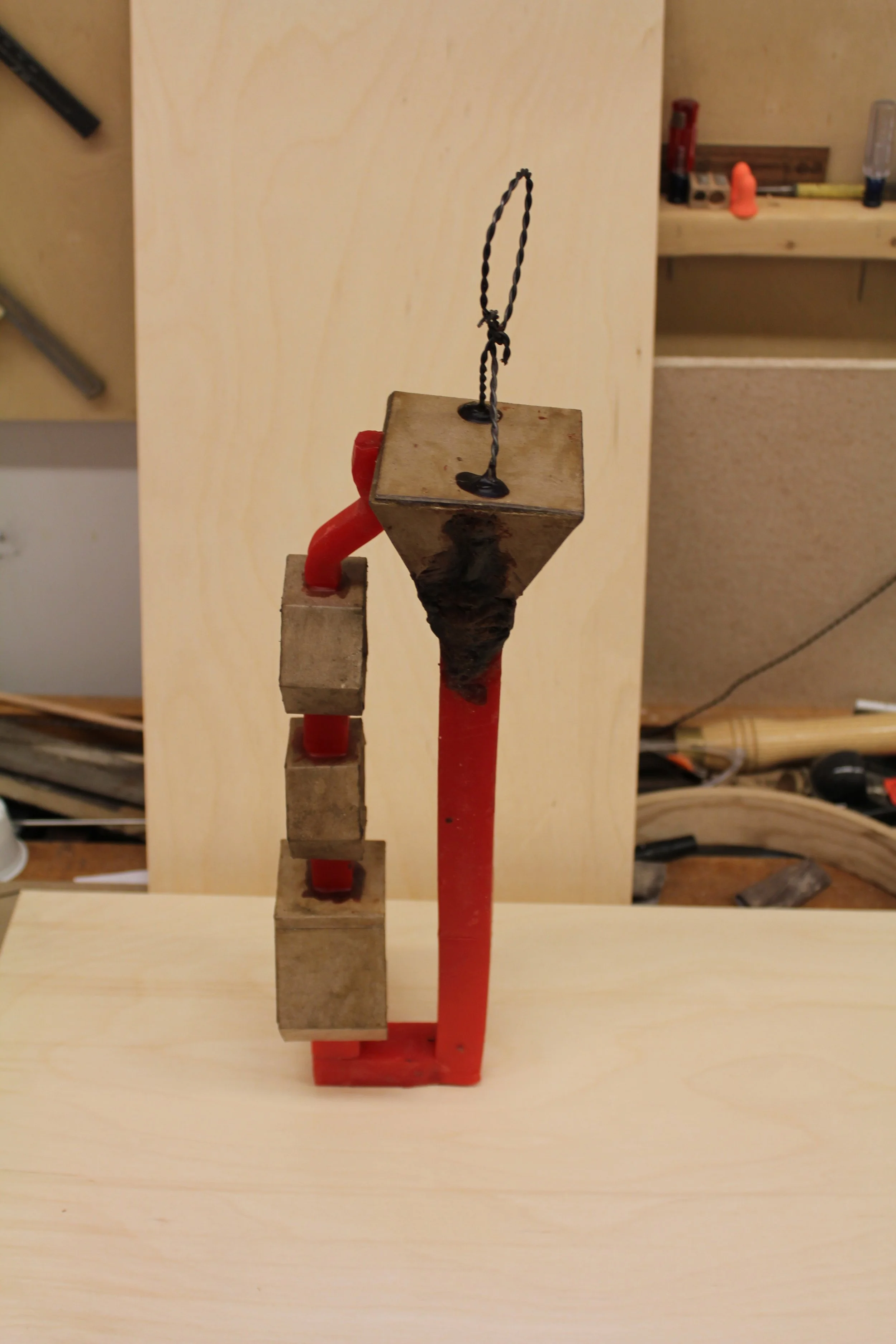

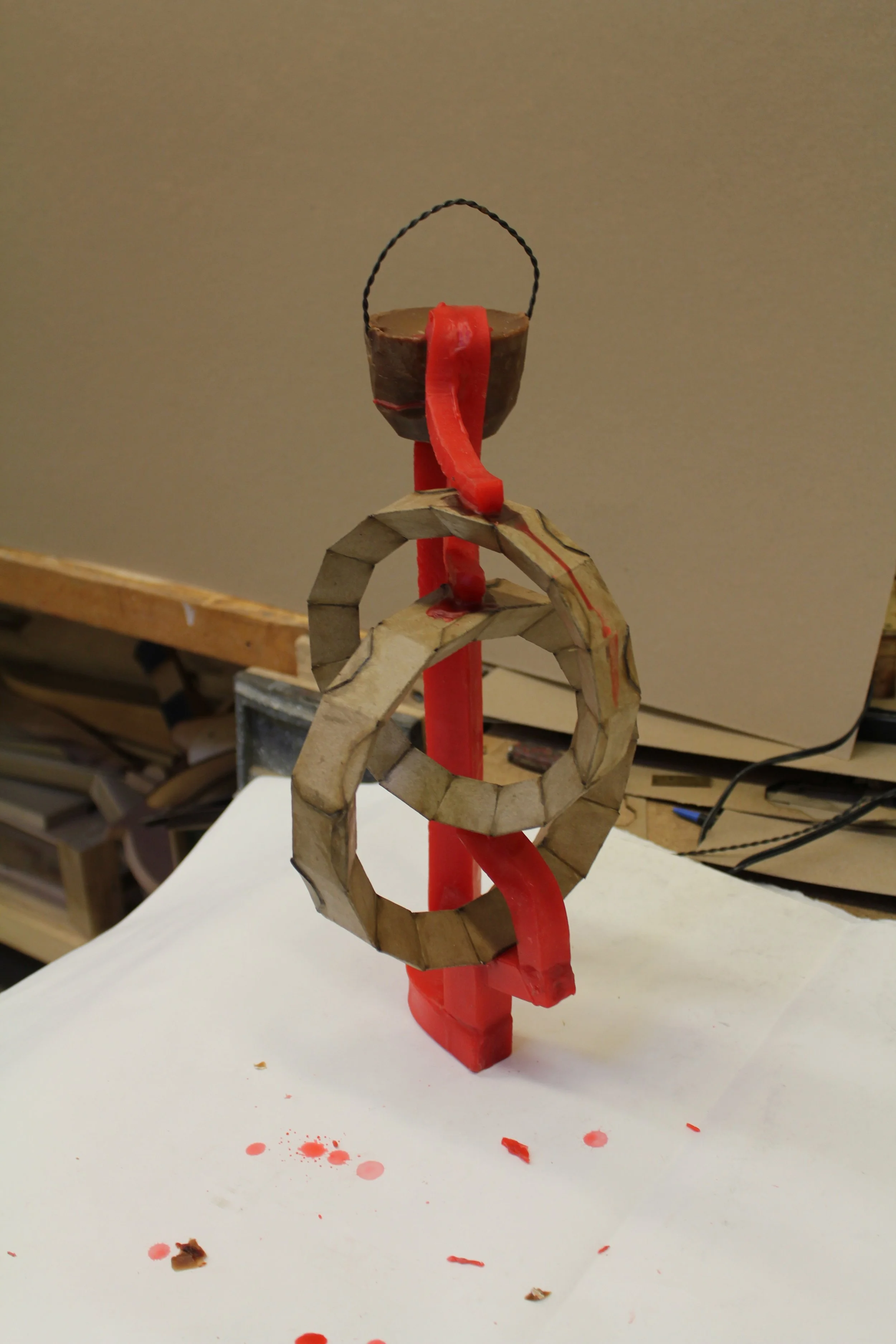
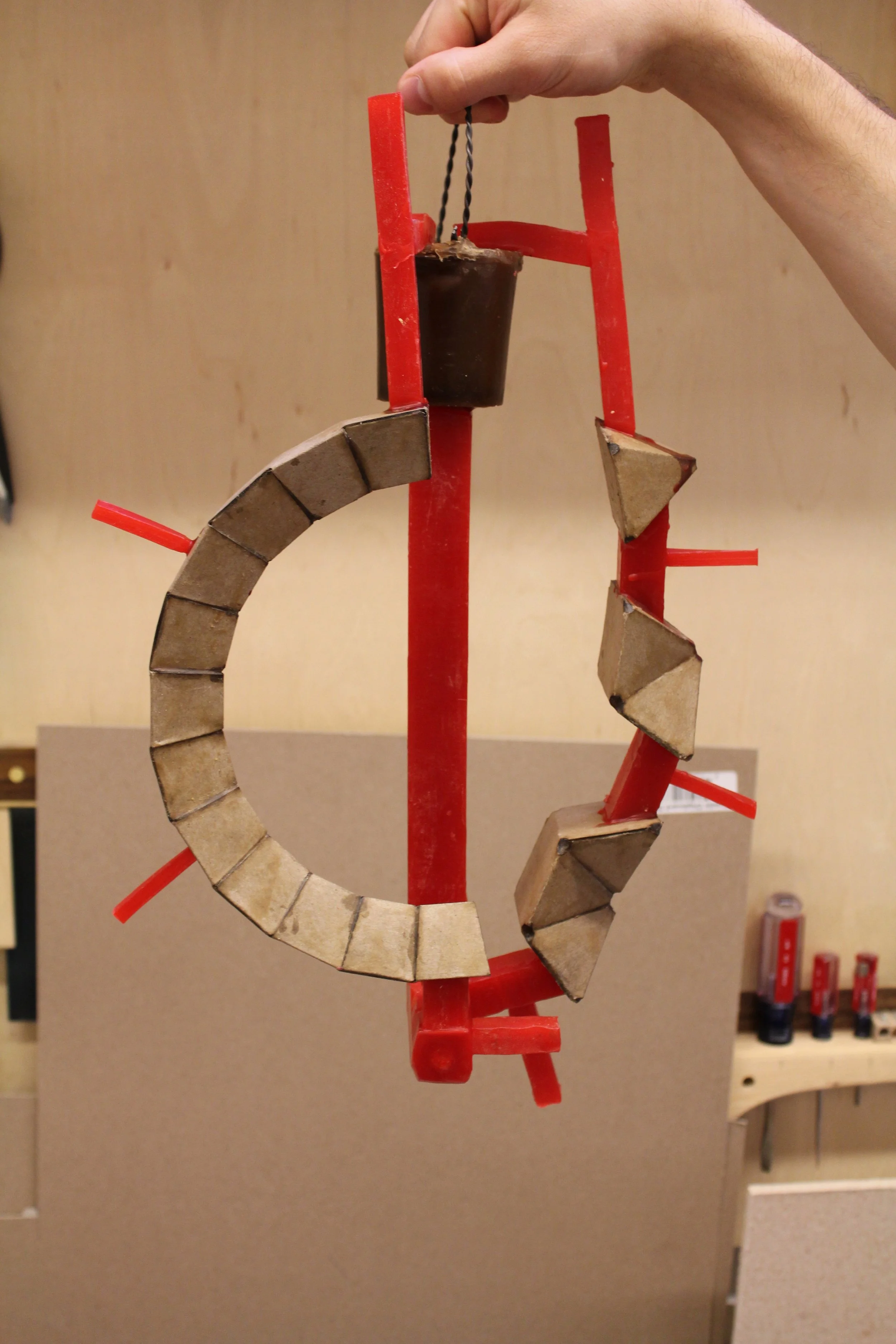

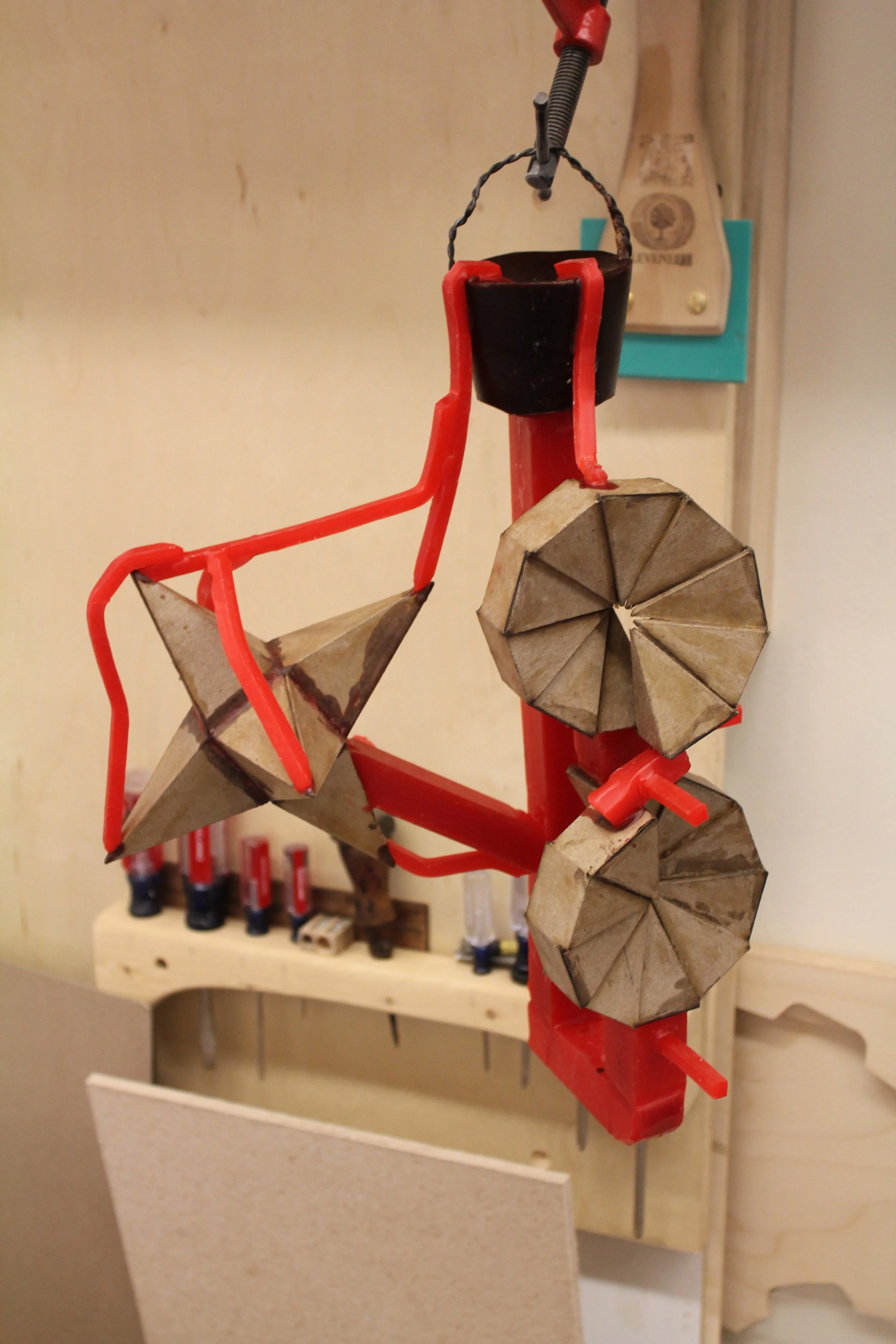
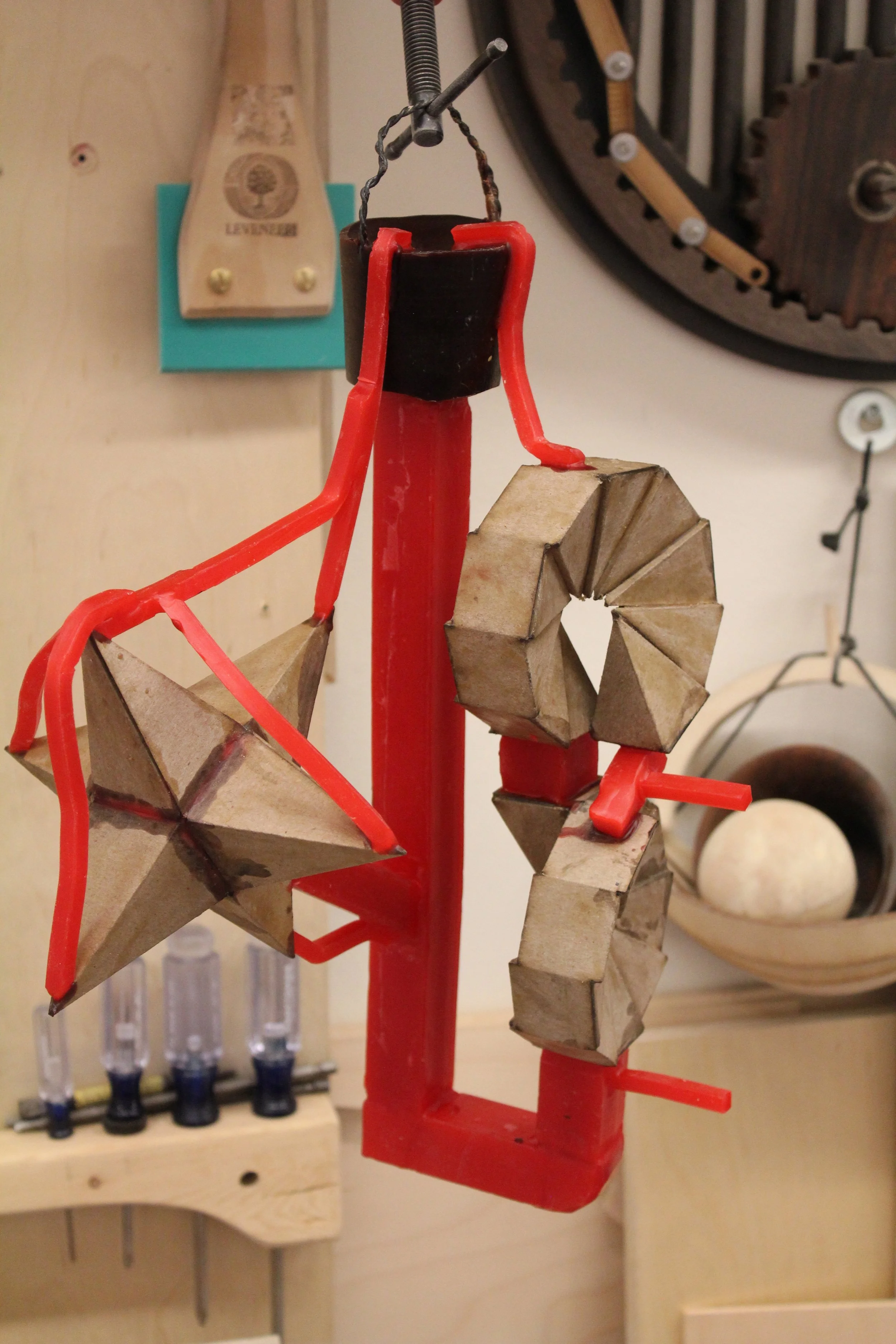